
The philosophy of the design method is that a lift-drag polar was first defined according to the requirements of a designed airfoil and then a pressure coefficient distribution along the airfoil was deduced.
#AIRFOIL DESIGNS CODE#
From the seventies of last century, NASA began on working with airfoil design using a code developed by Eppler and Somers.
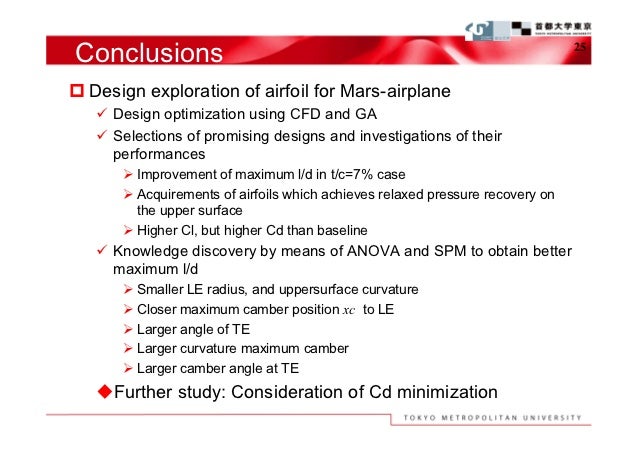
Introductionĭesign of airfoils for wind turbine blades is a very basic and important task for designing wind turbine rotors. Three new airfoils CQ-A15, CQ-A18, and CQ-A21 with a thickness of 15%, 18%, and 21%, respectively, are designed with the new integrated design method. In the optimization step, drag and lift force coefficients are calculated using the XFOIL code. As airfoil shapes are expressed with analytical functions, the airfoil surface can be kept smooth in a high degree. Using the trigonometric expression for airfoil profiles, a so-called integrated design method is developed for designing wind turbine airfoils. To validate and show the generality of the trigonometric expression, the profiles of the NACA 64418 and S809 airfoils are expressed by the present expression. As a direct consequence, three generic airfoil profiles are obtained from the expression. The characteristics of the coefficient parameters in the trigonometric expression for airfoils profiles are first studied.

#AIRFOIL DESIGNS SERIES#
As a main component in the design method, airfoil profiles are expressed in a trigonometric series form using conformal transformations and series of polynomial equations. A new method for designing wind turbine airfoils is presented in this paper.
